Measuring principles used for liquid measurement and detection
The capacitive measurement principle
At HB products most of our switches and level sensors are based on the capacitive principle which is well suited for refrigeration systems. The measurement principle was developed in the 1940’es and has been optimized since then.
HB Products has 25+ years of experience in the development of electronic sensors, originally for the refrigeration industry, for use with Ammonia, and today we evolved our sensor technology to work with all refrigerants.
A capacitor is formed when a level-sensing electrode is installed in a vessel. The center rod acts as one electrode in the capacitor and the reference tube or vessel acts as the second electrode. As the level rises, the air or gas normally surrounding the electrode is displaced by liquid having a higher dielectric constant. The measured capacitance (pF valve) is converted by the HB sensor electronics into either an analog 4-20 mA output signal or a dig- ital ON/OFF signal. All electronics are factory calibrated to specific fluids.
The capacitance relationship is illustrated with the following equation:
The dielectric constant (relative permittivity) is a numerical value on a scale of 1 to 100, which relates to the ability of the dielectric (material between the electrodes) to store an electrostatic charge. The dielectric constant of a material is determined in an actual test cell. Values for many materials are published. In actual practice, a capacitance change is produced in different ways, depending on the material being measured and the level electrode selection. However, the basic principle always applies. If a higher dielectric material replaces a lower one, the total capacitance output of the system will increase. If the electrode is made larger (effectively increasing the surface area) the capacitance output increases. Level measurement can be organized into two basic categories: the measurement of non-conductive and conductive fluids and materials.
Plastics, CO2, Oil and most syntetic refrigerants has a dielectric constant lower than 10, and they are defined as Non-Conductive. Ammonia, metals and water has a dielectric constant higher than 10, and they are conductive with a conductivity value at minium100 µS/cm.
When a capacitive sensor is used in ammonia and other conductive liquids one of the electrodes needs to be covered by a non conducting material to avoid shortening. Practically most capacitive level sensors and switches for conducting medias like ammonia are covered by PTFE which isolate the electrode electrically but still makes it possible to measure the level. Sensors with a PTFE covered electrode can be used in most syntetic refrigerants but not in oil, CO2 and hydrocarbons like propane.
Other measuring principles
In the refrigeration industry, several types of level transmitters are used to measure the level of refrigerants and oil, in tanks or vessels.The choice of level transmitter depends on factors like the type of liquid, the tank's design, environmental conditions, and the accuracy required. Here are some common types of level transmitters used in refrigeration applications:
Float Level Transmitters:
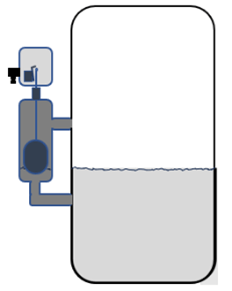
Float level transmitters use a buoyant float that rises and falls with the liquid level. As the float moves, it actuates a switch or a potentiometer to generate an electrical signal, indicating the level of the liquid. It is a low-cost solution, but the mechanical components have a risk of being worn out over time.
Radar Level Transmitters:
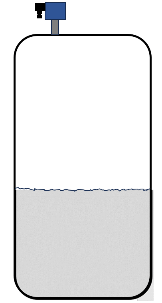
Radar level transmitters use microwave or radiofrequency signals to determine the distance to the liquid surface. By measuring the time taken for the signal to return, these transmitters can accurately calculate the liquid level. The regular radar transmitter requires a regular still liquid surface which can be a challenge in a refrigeration system.
Guided Wave Radar Level Transmitters: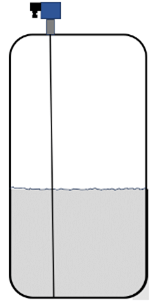
Guided wave radar level transmitters combine radar technology with a waveguide to direct and measure radar signals along a probe inserted into the liquid. This allows for accurate level measurement, even in challenging conditions. Low dielectric liquids like CO2 are difficult to measure.
Differential Pressure Level Transmitters: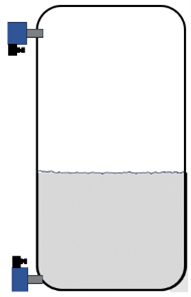
Differential pressure level transmitters use two pressure sensors—one at the bottom of the tank and one at the liquid's surface. The difference in pressure between these two points is used to calculate the liquid level. This sensor requires a relatively steady pressure.
Conductive Level Transmitters: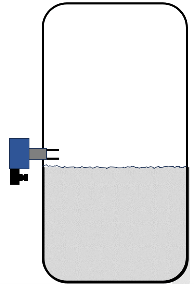
Conductive level transmitters use the electrical conductivity of the liquid to determine its level. When the liquid level reaches a specific point on the probe, it completes an electrical circuit, generating a signal.
Optical Transmitters: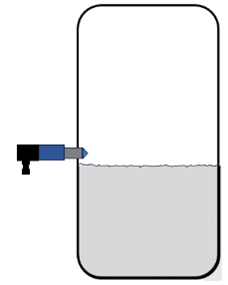
Optical transmitters are used as switches for detecting a level, but they are sensitive to pollution of the liquid and the sensor surface.
The choice of level transmitter depends on the specific requirements of the refrigeration system, including factors like the type of liquid being measured, the tank's size and shape, the need for continuous or point level measurement, and the desired accuracy and reliability. Advances in level measurement technology have led to the availability of various options suitable for different refrigeration applications.